The Fundamentals of Lofting a Bed
When I was designing our 200 sq foot cabin, an important element was the sleeping loft. This concept is common in the plans of many tiny houses. The fact that a double to king-sized bed eats a lot of space is obvious. Some smaller floor plans are greatly compromised by the 35 to 40 sq feet of space needed for a full-sized bed. Moving this part-time necessity up and out of the way makes room for other, more practical items. In my cabin the space below the loft functions as a dining nook, used primarily at sitting level, where the reduced headroom does not pose much inconvenience.
Free-Standing vs. Built-In Bed Lofts
In practically every tiny house plan I have ever seen, lofted bed areas are built in. The bed itself is normally just a mattress or futon-type pad set directly on the floor of this loft. Using a bed frame of conventional height is not practical due to limited vertical clearance. The advantages of a built-in include stability and robustness. The framing of the platform is just as sturdy as the rest of the structure. In many designs this loft area even improves the rigidity of the entire structure, as collar ties and ceiling joists do in larger buildings.
Freestanding bed lofts have the advantage of being portable, temporary and often multipurpose. I have seen versions that allowed dual bunk-type configurations or included desks or sitting accommodations below.
Back in my long-ago college days, I had a nice lofted bed in my dorm room. Here freestanding was the rule, as any “attachments” to the walls or ceiling were strictly forbidden. In those days, there were some good designs, as well as a few pretty scary ones. A safely built, sturdy unit requires common sense in addition to certain structural necessities. Common in the quick and cheap poorly built designs of that time were simple long-legged bed frames, often made from basic 2 x 4 lumber without the needed diagonal or cross bracing needed to prevent “racking.” Some were braced by wedges or large shims installed between the lofted bed and the cinder blocks of the walls.
One of the main drivers back then was cost savings. After all tuition, books, pizza and beer required financing, too. My particular loft was built from rough sawn timbers of 2 x 6 and 2 x 8 lumber. I used diagonal cross braces and bolted the entire structure together rather than simply nailing it. Although now I am an experienced woodworker, I wouldn't change the design much. Prior to building mine, I had the opportunity to view a good number of designs. My analytical mind quickly differentiated the ones that “worked” from those which were just thrown together. Mine cost a bit more but I was able to sell my loft to recover some of my initial expenses. Many of the lesser designs ended up in Dumpsters or as firewood.
Modern Versions of Bed Lofts
Today it is pretty easy to find plans, kits and even completed outfits online. Their quality usually correlates to their price. Simple steel imported units occupy the lower end of the market, while solid hardwood and more complex designs fill the upper tiers. Units that include integrated desks are still my favorite as they provide two functions, in addition to lower support and added structural elements.
The most common users of lofted beds are typically young. These range from grade school children who share a room with siblings and simply need the added space for a desk or relaxation area, to 20-something individuals living in dorms or basic economy apartments which are short on space.
As an older adult, I can still climb the ladder to use the loft at our cabin, but most of the time it is reserved for my teen and preteen daughters. The dining space below converts to a full sized bed as well … and from there it is much easier to stoke the wood stove in the middle of the night.
Kevin Stevens writes for Networx.com.
Updated April 5, 2018.
Looking for a Pro? Call us(866) 441-6648
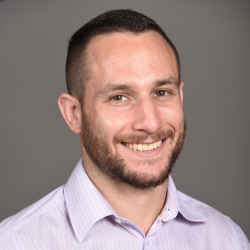
Remodeling Average Costs
Remodeling Contractors Experiences
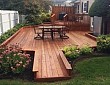
Professional Stain Adds The Finishing Touch To My New Cedar Deck
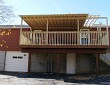
New Stairs And Roof Installation Are The Perfect Deck Upgrade
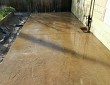